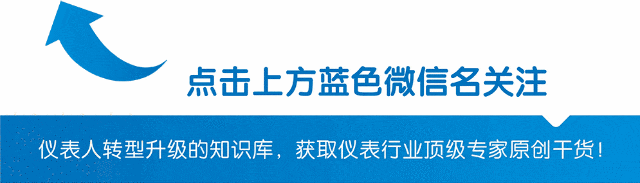
随着我国经济高速发展,化石燃料消费逐年增加,能源和环境问题日益凸显。大力发展清洁能源及可再生能源技术,既是“碳达峰”“碳中和”任务的迫切需求,又关乎国家能源安全与发展战略。在众多能源形式中,氢能被认为是21世纪“终极能源”,可以有效解决化石能源产生的诸多问题。通过风、光、水等可再生能源产生的氢气即“绿氢”,被认为是真正零碳排放的氢能,其核心技术电解水制氢已发展成为低成本、高效率的制氢技术。同时,电解水制氢技术为风、光、水等可再生能源长期以来存在的波动大、分布散、储存难等问题提供了极具前景的解决思路。
01
电解水制氢技术主要环节及我国现状
主要环节
完整的电解水制氢-储氢-供氢全产业链通常包含以下主要环节:
1)制氢,基于电网与可再生能源的电解水制氢;
2)储氢,基于物理、化学作用的多种氢气储存释放技术;
3)运氢/供氢,基于物流、管路的氢气储运技术以及分布终端;
4)用氢,以直接燃烧、化工原料、燃料电池底物等为代表的终端氢能利用方式。
我国现状
目前我国电解水制氢-储氢-供氢的发展正处于起步阶段,研究侧重于单独的电解水制氢、储运氢、供氢和氢应用技术的开发,仅在光伏发电/风电电解水制氢方面建设了少量的规模级应用示范。
在水电方面,我国至今还未建成示范运行的水电制氢基地,水电制氢的技术及成本问题还需要进一步解决。可以看出,我国在氢能利用领域有巨大的市场潜力,现阶段已形成初步的产业规模,然而对于氢能工业体系,制氢-储氢-供氢一体化产业链尚不完整,各个环节之间的技术发展相对独立,缺乏完整的系统设计与集成设施。
电网-氢能的制/储/供-用户联合的开式运行模式能积极推动氢能上下游产业链的发展与布局,为氢能的转型升级储备技术。但目前我国尚未形成制氢-储氢-供氢的全产业链条,还有待突破以下关键技术:
1)需强化氢能制备、储运、供应消费各个环节之间的有机关联,逐渐形成完整的技术与产业链条。
2)探索新型电解水制氢-储氢-供氢技术耦合电力系统的发展策略,深化氢能在电网储能、调峰、多元化应用场景中的渗透。
3)需继续加强电力系统与氢能产业的顶层设计、氢能关键核心技术攻关和人才培养,建立和完善氢能标准体系,加强国际交流合作,实现电力系统与氢能融合式高质量发展。
02
电解水制氢-储氢-供氢技术发展
电解水制氢技术
电解水制氢基本原理是:在直流电作用下,通过电化学反应将水分解为氢气和氧气。目前电解水技术可分为碱性(alkaline,ALK)电解水、质子交换膜(proton exchange membrane,PEM)电解水、碱性阴离子交换膜(alkaline anion exchange membrane,AEM)电解水和固体氧化物(solid oxide electrolysis cell,SOEC)电解水技术。
1)碱性电解水技术
碱性电解水技术以KOH、NaOH等碱性水溶液作为电解质,通过电化学反应将水分解为氢气和氧气。一般碱性电解水的工作电流密度约为0.25A/cm2,电解效率约为60%,运行温度较低(60~80℃)。碱性电解水技术的核心是碱性电解池,关键部件是以镀镍的铁电极或镍系金属制备的电极为基础,以石棉布和聚酯系等多孔材料为分隔膜。
在碱性电解池运行过程中,空气中的CO2会与电解液(KOH、NaOH)反应生成难溶的碳酸盐,如K2CO3。这些碳酸盐的沉积会导致多孔催化层的堵塞,阻碍液相和气相反应物、产物的传递,极大地增加了电解池的传质损失,降低了电解池的性能。碱性电解水技术较为成熟,投资成本低、运行寿命长且操作简单,已充分实现产业化,我国相关技术和产品都处于国际先进水平。但是该技术能量转化效率低,存在渗碱污染环境问题,需要对碱性流体进行复杂维护。另外,电解槽需要升温至工作温度才能开始产氢,导致电解槽启动准备时间较长,而电解槽从低温、小功率点往高温、大功率点调节时也需要温升匹配,导致制氢的产生速率难以快速调节。同时,电解槽最低运行功率不能低于额定功率的20%~25%,主要是由于在电解槽运行过程中必须严格控制电解槽的阳极和阴极两侧上的压力,防止生成的氢气和氧气通过多孔分隔膜在电解池阴极和阳极间互串,从而降低电解槽的法拉第效率,同时防止气体互串导致的爆炸风险。因此,碱性电解池在电力频繁波动的可再生能源系统中应用存在极大挑战。
2)质子交换膜电解水技术
在质子交换膜电解水技术中,通过质子交换膜传导质子并抑制阴阳极气体的互串,从而极大地避免了碱性电解池气体跨膜传递的缺点。水分子在阳极上氧化,生成质子、电子和气态氧,质子通过交换膜到达阴极,电子通过外部电路传导,在阴极将质子还原生成氢气。典型的质子交换膜电解池主要由阴阳极端板、气体扩散层、催化层和质子交换膜构成。端板主要起到固定、支撑和集电器作用,同时引导气体和水的传递和分配;气体扩散层主要是促进气液相反应物的传递;催化层是电解水反应发生的场所;质子交换膜作为固态电解质起到传导质子和隔绝气体互串、电子传递的作用。
需要注意的是,质子交换膜电解池的组装可采用零间隙结构,使得电解池的结构较为紧凑,能有效降低电解池的欧姆电阻、增加输出电流。因此,质子交换膜电解池的工作电流密度可高达1A/cm2,至少是碱性电解池的4倍。同时,由于质子交换膜作为分隔材料,使得质子交换膜电解池产氢纯度高达99.999%。此外,质子交换膜电解池在5~80 ℃都可运行,启动时间仅为毫秒级,可快速启停,且由于质子交换膜的隔离,避免了阴阳极产生的氢氧互串,使得电解池的工作范围可在整个负载内变化。
然而,质子交换膜电解池常用的催化剂主要是Ir、Ru等贵金属,导致其加工制备的成本较高。目前,质子交换膜电解池已经初步进入商业化阶段,开展了一系列小型示范;虽然成本偏高,但随着市场规模增大、电极材料的研发,有望逐步实现商业化。
3)固体氧化物电解水技术
固体氧化物电解水是固体氧化物燃料电池的逆反应,通常在700~850 ℃的高温下运行。由于在高温运行条件下,电极具有较好的反应动力学性能,因此可使用廉价的镍基电极。固体氧化物电解池阴极常采用Ni/YSZ多孔陶瓷材料,阳极主要采用钙钛矿氧化物,中间电解池则采用YSZ氧离子导体。固体氧化物电解水基本原理是:当高温水蒸气进入固体氧化物电解池时,在阴极被分解为质子和氧离子,质子得电子后被还原生成氢气;氧离子通过固体氧化物电解质传递到阳极后,被氧化生成氧气。由于固体氧化物具有较好的热稳定性和化学稳定性,高温条件下电解池所需电压较低,制氢效率可高达90%以上。需要注意的是,通入阴极的水蒸气一般需混有少量的氢气以保证阴极的还原气氛,防止阴极材料氧化。然而,由于电解池在高温高湿的条件下运行,电极材料的耐久性是目前亟待解决的问题,运行过程中的热化学循环,特别是系统启停都会加速电极老化,降低使用寿命。总体来看,固体氧化物电解水制氢效率高,但工作温度高、寿命低、启停繁琐,目前仍处于示范阶段。
4)碱性阴离子交换膜电解水技术
碱性阴离子交换膜电解水技术作为最新的电解水技术,可同时结合碱性电解池的低成本与质子交换膜电解池的结构紧凑、简单高效等优势,具有较大的研究和开发潜力。碱性阴离子交换膜电解水技术能使用非贵金属作为电极催化剂,并且能在阴阳极腔室压差下运行。然而,目前阴离子交换膜面临化学、机械稳定性不足的瓶颈,使用寿命问题依然未得到解决。另外,阴离子交换膜的离子传导性较质子交换膜差,导致电解池反应较慢,电解结构不佳。通过添加支持电解质虽然能提升膜的离子传导性,但又影响了使用耐久性。有研究[20]指出,质子交换膜中OH-离子的传导速率要比H+质子慢3倍,这意味着阴离子交换膜的开发面临着更大的挑战,需要研制厚度更小、电荷密度更高的膜。虽然阴离子交换膜电解池工作温度低、可快速启停,但目前尚处于实验室研发阶段,短期内难以实现大规模商业化应用。
在上述4类电解水技术中,使用固态质子交换膜替代碱性电解池中液态电解质和分隔膜,能够将氢气和氧气分隔开,防止气体互串,气体纯度高。同时质子交换膜电解池具有电流密度大的优势,可快速启停、负荷范围宽,能够与波动性大、间歇性强的光伏、风电等可再生能源进行较好的匹配。将质子交换膜电解池与可再生能源电解直接耦合,有望适应未来快速增长的大规模风电、光电等可再生能源制氢需求。
储氢技术
不同的电解水制氢方式所产生的氢气在纯度、压力上存在差异。除一些特定场合需要制氢后立即使用外,产物氢气均需要经过纯化与储存才能满足终端用户需求。相比于纯化过程,储氢过程在技术上更复杂,在整个氢能产业链条中尤为关键。
1)高压气态储氢技术
压缩氢气在环境条件下通过高压将氢气储存在压力容器中,是一种应用广泛、简便易行的储氢方式,现阶段发展成熟且广泛使用。其成本低,易于储存和释放氢气,且在常温下就可以进行。以现有的小规模车载储氢罐为例,其工作压力为35~70MPa,对应的氢气密度为0.039kg/L,远大于自然条件下的氢气密度(8.1×10-5kg/L)。高压储氢技术的限制因素主要来自两方面。一方面是氢气的压缩能耗及储存压力,目前大量应用的隔膜压缩机可实现22~32MPa的充装压力,加氢站压缩机可实现45MPa以上的高压。然而当压力增大至70 MPa后,氢气性质开始大幅偏离理想气体,若继续增加压力,储氢的收益将降低,会浪费大量的压缩功。另一方面,高压氢气需要耐压容器进行储存,容器加工制造成本是另一个主要限制因素,现有高压储氢容器包括全金属气瓶、复合纤维材料缠绕气瓶、复合材料储氢罐、玻璃储氢容器等。尽管现阶段有多种容器材料可供选择,但其造价成本仍较高,难以规模化应用。此外,不同的使用场景中氢气泄漏和容器爆破等不安全因素也需要进行考虑,如高压气瓶的氢脆现象及其失效机制等。对于高压储氢技术,在不断提高其储氢密度、降低成本的同时,保证其安全性能是长远发展方向。
2)低温液态储氢技术
低温氢气液化与空气液化相似,在低温液态储氢过程中,先将氢气压缩,在经过节流阀之前进行冷却,经历焦耳-汤姆逊等焓膨胀后产生液态氢。把液体分离后,将其储存在高真空的绝热容器中,气体继续进行上述循环。与高压储氢相比,低温液态储氢密度高,液态氢的密度在常压下可达到0.070kg/L,约为压缩氢气的1.8倍,储氢质量大幅提高,其安全性也相对较高。但是由于氢气液化要消耗很大的冷却能量,液化1kg氢气需耗电4~10kW⋅h,液化氢气所消耗的能量约为同等质量氢气能量的30%,无疑增加了储氢和用氢的成本。另外,液氢储存容器必须是超低温用的特殊容器,由于液氢储存的装料和绝热不完善容易导致液氢蒸发,使容器内压力升高,因此必须将氢气排出,从而带来沸腾损失。综合而言,液态氢储存成本较高,安全技术也较复杂,民用领域少有应用,在航天领域,火箭助推剂是其主要应用场景。提高绝热技术效率将有助于进一步提高低温液态储氢效率,目前通过额外能量来实现传热的主动绝热技术是低温液化领域的研究热点,有望实现液态储氢容器内超低蒸发率乃至零蒸发率。
3)物理吸附储氢技术
物理吸附储氢技术依靠氢气分子与材料表面间的范德华力,将氢气分子吸附到材料表面,在一定条件下可实现吸附脱附转换,从而实现储氢。物理吸附储氢技术的核心是吸附材料,常用的吸附材料可分为碳基材料、有机金属骨架(metal-organic frameworks,MOF)材料、储氢水合物等。其中碳基材料价格相对较低,如碳纳米管(carbon nanotube,CNT)、介孔碳、碳气凝胶等。MOF是一类具有超大比表面积的新型合成多孔材料,目前常用的MOF材料有MOF-5、HKUST-1、MIL-53等,在液氮低温条件下,其饱和氢气吸附质量分数分别为5.1%、3.6%、4.5%。储氢水合物利用氢键连接形成空腔结构,氢分子以浆液的形式在其内部进行储存。通过结构分解进行氢分子的释放,但其本身稳定性较差,储存密度也相对较低,目前停留在实验室研究阶段。总的来说,物理吸附储氢技术由于其材料与氢分子的作用力相对较弱,需要在较低温度下进行储氢,其储氢密度较小,现阶段难以进行大规模的氢气储存与利用,一般将其与其他储氢技术相结合来实现复合储氢。对于物理吸附储氢技术,如何降低材料成本、提高材料循环利用率、增大储氢密度是其未来发展的瓶颈问题。
4)化学储氢技术
化学储氢利用化学反应,将氢气转化为其他化合物进行储存,包括储氢合金、化学氢化物、有机液体储氢等。储氢合金依靠某些金属或合金对氢气分子有很强的捕获能力,在一定条件下金属吸附氢气分子,氢气分子H—H键断裂,形成氢原子储存在金属或合金的晶格间隙中,形成金属固溶体并释放反应热。将这些固溶体加热到一定温度后,氢气能够被重新释放。储氢合金可以实现较大的储氢量,且稳定性和安全性较高,然而其稳定性使得氢气储存和释放比较困难,只能在高温下进行。氢化物储氢利用氢气与金属反应生成金属氢化物(如MgH2、CaH2、AlH3等),从而进行氢的储存。由于这类碱金属具有较高的活性,因此可以生成较为稳定的离子化合物,从而具有较稳定的氢气储存特性。然而其反应可逆性较差,运行条件苛刻,需要在较高的温度和压力下进行储/放氢,目前仍难以实际应用。有机液体储氢利用不饱和液体有机物与氢气之间的可逆反应,采取催化加氢-脱氢过程来实现氢气的储存和释放,具有储氢量大、安全性高、可多次循环等优点。然而,由于加氢脱氢反应控制条件严苛,成本高,且副反应难以完全抑制,氢气纯度较低,因而限制了其规模化应用。总体而言,化学储氢具有较高的储氢密度及稳定性,优化其反应动力学特性、实现温和的操作条件,将有助于其早日实现规模化应用。
供氢技术
加氢站是电解水制氢-储氢-供氢系统中的末端供氢设备,是氢能产业发展的核心基础设施之一,特别是对氢燃料电池汽车以及氢能技术推广而言,加氢站的建设显得尤为重要。不同制氢及储氢技术转化为用户氢源时,所需要匹配的加氢站不尽相同,目前较为典型的加氢站包括撬装加氢站、固定式加氢站、液氢加氢站和制氢加氢一体站。
1)撬装加氢站
撬装加氢站主要分为不含固定储氢装置的撬装加氢站和含固定储氢装置的撬装加氢站2种模式。其工作流程如下:氢气长管拖车将氢气运输至加氢站后与卸气柜相连接,随后氢气进入压缩机内被压缩,通过顺序控制柜输送至储氢瓶组中进行分级储存。当需要进行加注服务时,氢气通过储氢瓶组至顺序控制柜再到加氢机为用氢设备进行加注。上述2种模式主要区别在于是否含有固定的储氢瓶组,对于不含固定储氢装置的撬装加氢站,随着氢气长管拖车中余气压力下降,撬装压缩加氢装置加注速率逐渐降低,使得加注时间延长;含固定储氢装置的撬装加氢站加注速率不受限于压缩机的排量,从而提高了加注效率和速率。总体来说,撬装加氢站的特点是可灵活定制,将重点设备进行系统集成整合,占地面积小,投资成本低,施工工期短,设备安装方便,能在短时间满足客户的加氢需求。然而,撬装加氢站的压缩机和加氢机设置在同一区域,具有一定的安全隐患,因此,目前该类加氢站只作为临时站点,今后将会被固定式加氢站所取代。
2)固定式加氢站
相比于撬装加氢站,固定式加氢站不依靠长管拖车,而主要是将站外0.4~2.0 MPa的氢气通过管道引入站内,同时还增设了2组高低压压缩机。其工作流程如下:氢气先从氢气管道中进入缓冲罐,然后进入20MPa压缩机内被压缩,部分氢气随后进入充装柱,再注入氢气长管拖车,剩余氢气进入45MPa压缩机内被压缩,提高压力后被输送至储氢瓶组中储存供使用。
固定式加氢站主要是为氢燃料汽车及其他潜在客户提供加氢服务,采用氢气管道进行供氢,具有无交通运输限制、无道路运输成本和氢源更稳定的优势,但是一方面由于要添置高低压压缩机和长距离的氢气输运管道,建设成本高;另一方面,由于其氢源通常来源于工业副产氢,使得其氢气纯度不稳定。
3)液氢加氢站
由于液氢密度是标准状态下氢气的800倍左右,储氢密度高,采用液氢储氢后,加氢站的储氢能力和加注能力将大幅度提升。液氢加氢站工作流程如下:液氢槽车将液氢运输至加氢站并接入液氢储罐,液氢储罐中的氢通过泵的增压和气化器的气化后进入储氢瓶组供使用。液氢加氢站由于液化消耗了大量冷却能,另外,液氢储存容器必须使用超低温特殊容器,而液氢储存的装料与绝热不完善导致较高蒸发损失,也增加了其储存成本。
4)制氢加氢一体站
上述3种加氢站都属于外供氢加氢站,随着用氢规模提升,运输成本必然增加。制氢加氢一体站可同时解决氢源不足和运输成本过高的难题。目前,制氢加氢一体站的制氢方式主要有电解水制氢和天然气重整制氢。
站内电解水制氢技术的主要特点是:只要水和电等原料满足供应,即可实现电解水制氢,若考虑利用电网谷电进行电解水制氢,则可进一步降低制氢成本。天然气重整制氢是目前最为成熟的工业制氢技术,因此,站内天然气重整制氢加氢站的建设最有保障。其工作过程如下:脱硫后的天然气和水蒸气在高温和催化剂的条件下在重整装置中反应,生成的氢气、一氧化碳以及二氧化碳通过变压吸附(pressure swing adsorption,PSA)装置将氢气分离出来,然后纯化供使用。
目前制氢加氢一体站的推广仍然需要考虑如下问题:
①如何将制氢设备一体化和小型化;
②电解水制氢耗电量较大,电能紧缺地区使用将受限;
③当制氢加氢一体站体量较小时,其经济性仍需要评估。
除了上述加氢站外,含加油、加气、充电等功能中一项或几项的加氢合建站也在陆续规划中,同时由于液氢加氢站储氢密度优势明显,随着氢液化相关技术的逐步攻克和国产化,液氢生产成本也将进一步降低,因此液氢加氢站将可能成为加氢站技术新的发展方向。