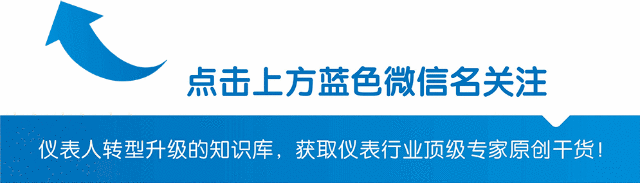
冶金转炉炼钢技术是我国工业发展过程中的一项重要工艺,其在生产工艺上具有较高要求,要实现冶金转炉自动化控制技术,对冶金设备提出了极高的要求。目前,我国大部分钢铁企业的生产线都具有先进的水平和成熟的经验,但在实际操作过程中,仍然依赖技术人员手动操作,导致了生产效率较低,人员的劳动强度偏大。同时,在生产过程中会产生大量的有毒有害物质和危险源等,很可能造成安全事故。为此,发展自动化炼钢尤为重要。但是,现行的自动化炼钢技术存在诸多不足,如设备复杂、操作繁琐,工序间缺乏沟通与配合,设备数量多且分散,导致转炉炼钢自动化技术发展缓慢。因此,解决实际生产中转炉炼钢自动化工艺控制的影响因素至关重要。
01
冶金转炉炼钢自动化控制技术现状
转炉炼钢自动化控制系统以冶金设备为主,通过对转炉炼钢中的参数进行检测,使其达到生产终点的控制值。虽然现阶段我国钢铁工业发展迅速、生产技术和产品质量不断提升,但生产装备的自动化程度不高,导致智能化运用在转炉炼钢方面应用水平不高。
因此,需要在这些领域进一步推广和使用智能化程度较高的冶金设备自动化控制系统,以便适应市场需求和企业生产管理方式,逐渐改变自身落后状态。
转炉炼钢自动化控制系统利用计算机技术、自动控制等原理,在现场的转炉炼钢过程中,通过对各种参数(包括的氧枪枪位、铁水成分、铁水温度、冶炼过程的煤气发生量、升温速率、辅料加入时机)进行实时监控,实现生产过程自动化。该系统可以提高工作效率,降低工人劳动强度。其特点有:
(1)具有较高的可靠性;
(2)一键操作;
(3)成本低且功能齐全、使用方便;
(4)便于维修管理;
(5)性价比更高。
转炉炼钢自动化控制系统主要由传感器与控制器组成,利用PLC控制技术,在现场生产中进行检测、监视、报警等。该系统具有以下功能:实时监控设备运行参数;自动判断故障部位及原因,及时发出警报提示工作人员;通过PLC控制系统实现自动化控制功能,同时可以增加人工干预功能,现场作业可以根据实际情况调整工艺流程与操作规范,以提高产品质量、降低成本费用支出等。
02
冶金转炉炼钢自动化控制
技术存在的问题
炼钢自动化控制存在的矛盾
转炉炼钢自动化技术是一项先进的现代化工业技术,其在我国钢铁行业中占有重要地位。但由于目前大多数企业对生产过程控制存在认识误区,导致实际应用效果不佳、效率低下等问题日益突出。尤其是部分员工思想观念落后、缺乏责任感,使生产线运行质量差且难以满足客户需求,出现质量事故,严重影响了冶金转炉炼钢自动化工艺流程化管理水平的提升。
转炉炼钢自动化控制技术的应用,对冶金企业来说是一个挑战,其主要体现在:第一,设备数量多且分散,导致转炉炼钢自动化技术发展缓慢。第二,企业担心自动化控制系统的稳定性,设备投入运行之初,需要长时间磨合,无法实现达产达效,不能带来足够的经济利益,同时,系统运行过程中存在一定风险,容易引发质量、安全事故等问题。
炉温偏差
受热不稳定、温度变化等各种原因影响,炉膛内温度过高或过低,会导致转炉烟道结渣、结瘤,严重减少设备的使用寿命。而当其与负荷相匹配时,就会产生过热现象。所以,要想使冶炼过程顺利进行并达到相应的质量水平,必须严格控制炉温偏差并采取措施解决这些问题。
转炉炼钢自动化技术的关键点是控制转炉的钢水成分和温度。如果能实现准确测量与实时监控,就可以实现冶炼过程的稳定控制,从而满足钢水成分和温度控制要求。利用计算机系统控制冶炼过程的操作流程,以此收集数据,建立冶炼过程大数据库,并建立一个动态监测模型,对其温度、压力等参数进行分析判断后做出相应决策,调整控制设备和装置的运行状态,从而实现自动炼钢。
炼钢自动化控制的难点
冶金转炉炼钢自动化技术在实际生产过程中,受多种因素的影响:首先,环境问题。冶金厂转炉炼钢复杂、高温高压等特点,导致转炉炼钢的工作条件比较恶劣,会对设备产生不利影响;其次,工艺要求较高且复杂程度较大,对工人的技能水平有更高的标准和更严格性要求;最后,炼钢生产技术难度大,在实际作业中面临着控制点多、控制难度大、精度要求高、结果要求稳定等难点问题。
炼钢自动化控制系统不确定性
转炉炼钢的自动化生产系统非常复杂、庞大,要求技术人员具有较高的知识水平和技术能力。所以,在实际工作中很难准确把握其过程控制对象的数学模型、动态特性、对控制系统进行分析处理等内容。因此,在设计阶段需要根据现场具体情况确定所需设备的类型及参数。同时,还应结合现场的实际状况对工艺流程进行合理调整,并制定相应的保护措施,以确保转炉炼钢自动化系统正常运行,进而保证整个生产环节顺利完成工作任务。
转炉炼钢自动化控制系统的不确定性主要表现在以下两方面:一是受控对象的多样性;二是对环境条件和参数变化反应速度较快而引起工艺过程波动大时,会使转炉炼钢自动化控制系统的不确定性变大。