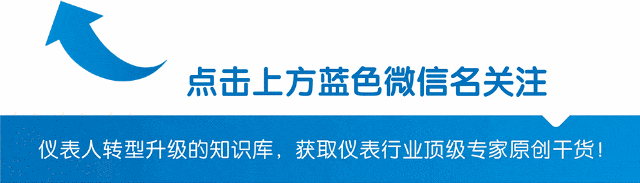
报警管理
在现代的控制室,由于DCS的广泛使用,产生了数量巨大的报警信号,且报警数据中存在大量冗余和虚假信息,因此导致在实际工厂运行管理过程中,对大量报警视而不见,使报警信息无法发挥最佳效果。
各行业报警管理现状及国际标准
目前DCS报警泛滥和不重视报警信息处理的原因一般包括:
报警级别设置不合理,存大量冗余报警,虚假报警,过量的高优先级报警,不同工况下不能及时应用新的报警设置值,以及缺乏有效的报警处理指导和专家库等。这些问题不仅会对操作员造成工作压力,而且会导致操作员对报警不敏感,疏漏重要报警,产生安全隐患。
因此,依托实时数据库、移动应用和数据分析算法等技术手段,建立“生产异常报警管理系统”,对生产过程中的报警、生产隐患等事件实现在线监测,采用报警分组、报警优先级、基于工况的报警、报警过滤、报警抑制等手段,实现生命周期的报警管理,充分发挥报警系统的功能,提高生产操作安全性。
02
操作员培训仿真(OTS)
对流程行业来说,往往存在人员流动大,缺乏有经验的技术人员等问题。传统技术人员的培养周期长、投入费用高。传统的培训模式是将操作员安排至同类工厂实习,大部分是在“看”,实践操作机会少,感受不到真实工厂环境的氛围,这对于新建设的工厂的员工培训说是极其不利的。
OTS系统中流程模拟设计软件的介入使快速培养高层次的技术人员成为可能。基于OTS系统的操作员培训模式,不仅技术上可行,而且能为工厂极大地节约外出技能培训费用、减少试车投产风险、带来可观的效益。其主要优势如下:
(1)通过流程模拟软件的培训与学习,技术人员深人掌握各种典型单元操作(如塔、换热器、炉子、反应器)的基础理论、工艺设计、设备设计、过程控制设计和操作方法。
(2)完成本装置的流程建模,实现物料平衡、热量平衡计算,核算原有设计是否最优及有多大优化的空间,确定优化点的优化效益,提出优化方案。
(3)制订出最佳开车方案、 危险与可操作性(Hazard and Operabilit,HAZOP)分析、事故应急方案。
(4)确定装置中各个设备的设计余量,确定装置最大操作负荷,确定操作的卡边界限。
(5)在装置考核阶段,对装置操作的实际能耗与计算能耗进行对比,对装置进行性能标定。
(6)在装置运行阶段,制订出典型工况的运行方案。
(7)对工艺过程的异常现象进行故障分析。
(8)完成工艺操作优化研究、先进控制研究。
OTS系统一般选择在工厂装置投产(开车)6-8个月之前建设完成,可作为生产工优化和测试的基础与工具,也可作为虚拟装置帮助开发、验证、调试工况工艺的功能模块,同时可利用系统对新人职员工进行操作培训。
03
优化控制
造成装置自控率不高的原因一般包括:在自动化过程中,流量仪表量程不够、低流量不显示、测量值波动大、瞬间归零等情况;生产装置采用的工艺包内有些控制方案不符合当前的工艺操作条件,需要完善或优化;部分装置PID参数范围过小,无法调节;测量仪表毛刺较大,影响到PID控制精度。
另外,通过结合三维可视化技术,还可以对工艺的生产过程建立模型,并与OTS系统关联,实现仿真、优化实时联动的生产流程指挥,所有工艺和操作数据都能在系统中实时监控,针对过程关键回路进行监控和诊断,包括对自控投用率、饱和、响应速度、振荡、迟滞、阀门移动行程、相对性能指数(RPI)等参数的控制性能监视,最终实现数字孪生的智能化、可视化操作新型运营模式。
04
先进过程控制(APC)
APC实施过程中的注意事项
在DCS常规控制的基础上,须结合PID回路整定,对部分生产装置实施APC,按先易后难、效益显著的原则实施。APC应用得好坏,关键由模型质量决定。由于实际工厂中的各种原因,工艺条件随着时间的推移总会发生一些变化,模型需要及时修正和更新。一般模型更新时间为3~5个月一次,需要专业队伍进行维护。
APG与PID控制区别
首先,APC与经典PID控制器的最大区别是不再只是对单个变量的控制,而是对被控对象的整体进行多个变量的控制;
其次,APC相较PID控制具有预测功能,可以根据多个回路工况进行分析,从而对控制器内的每个回路进行预测,可以让控制效果最大限度地得到优化;
再次,APC相较PID控制优化具有更强的适应能力和更好的鲁棒性。相较经典PID控制优化,APC策略采用多变量优化算法,适合处理多层次、多目标和多约束控制问题,能够更方便地反映生产过程的经济指标。
05
异常诊断
异常诊断大致可以分为基于机理模型的异常诊断、基于软仪表的异常诊断和基于工业大数据的异常诊断。
基于机理模型的异常诊断是最早研究的一种异常诊断方法,主要包括残差产生和残差评估两个阶段。但实际工业生产中,很多设备系统属于非线性多变量耦合的复杂系统,再加上实际生产环境非常复杂,有很多不确定因素及环境变化都可能导致机理模型低效或失效。因此,基于机理模型的诊断方法实际使用效果并不理想,应用范围有限。
现代工业对控制和可靠运行的要求越来越高,常规的温度、压力、流量等参数测量已经不能满足工艺和控制的精细化管理要求,还需要获取一些与过程和控制相关的检测参数。因此,基于软仪表的异常诊断越来越受到行业的关注。
可实现异常诊断的场景:
仪表异常预警和故障诊断。对于重要的仪表变量,建立仪表故障的预警诊断模型,判断除了智能仪表诊断以外的仪表故障,如仪表的冻结、跳变等,以及与工艺相关的故障判断,如物料平衡、能量平衡等。
调节阀预警诊断,如调节阀执行机构问题、调节阀芯与阀体问题、工艺条件变化对林公调节阀的影响等。
回路预警诊断,如回路模拟与优化、回路投用率与诊断分析、PID等。
工艺异常诊断,如原料组成变化、负荷变化、环境(包括公用工程)变化、反应条件变化等。
设备异常诊断,如阀卡、泄漏、阀堵(管路),换热器换热效率、泄漏、堵塞,塔干板、液泛等。
在化工生产中,自动化优化提升是必不可少的。你们企业的自动化优化提升是如何做的?欢迎评论区留言,分享经验,共同学习!↓↓↓